Gas lines can leak and cause a variety of problems. In order to minimize the risk, Local Law 152 requires a regular inspection of all gas line systems by an approved inspector.
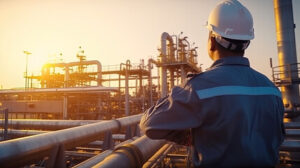
Only licensed master plumbers or those working under their supervision can perform LL 152 inspections. The resulting GPS1 must then be filed with the DOB by the building owner.
A gas leak is a serious issue that should be addressed immediately. These leaks can create carbon monoxide poisoning, fire hazards and other health issues. In addition, they can cause damage to a building and lead to costly repairs.
During a gas line inspection, licensed professionals can use various tools to identify potential leaks. Some of these include soapy water tests, electronic gas sniffers and ultrasonic leak detection systems. They can also perform a pressure test to detect a loss of pressure, which is a clear indication of a leak.
These tools are not only safe, but they can help to pinpoint the exact location of a leak. This allows property owners to get the leaks fixed before they cause any damage or pose a danger to anyone.
During the process, professional gas line inspectors can also check for proper ventilation. This ensures that the piping is not being used in an area that cannot provide sufficient ventilation, which can lead to a buildup of carbon monoxide and other gases. This is an essential step to ensure the safety of everyone in a building.
The inspector can also check the condition of the gas barrel and make sure that it is in good shape. He will also make sure that the gas barrel is placed in a suitable area where it can be stored safely. Lastly, he will also check to see that there is no rust or corrosion on the piping.
Once the gas piping inspection is complete, you will receive a GPS1 report from your licensed professional inspector. This report includes the date and time of the inspection and identifies the conditions that must be corrected in order to be in compliance with Local Law 152.
If there are any problems that surface during the inspection that require corrections, the property owner must remedy these conditions so that a Certificate of Correction can be filed within 120 days of the initial inspection. If the property is unable to be brought into compliance, a court hearing will be scheduled and the building owner could face a fine.
Check for Damage
During the inspection, the LMP will check for signs of leaks, corrosion, damage to protective coatings and any other issues that could put the system at risk. The LMP will also evaluate the condition of the pipeline’s valves, fittings and connections. He or she may use non-destructive methods such as ultrasonic testing and magnetic flux leakage testing to test the integrity of the pipe and locate any potential problems.
A comprehensive report is required to show the results of the inspection. The report should clearly describe the method(s) used and include a detailed analysis of the pipeline’s condition. The report should also contain recommendations for corrective action and/or ongoing monitoring.
Pipeline inspections can take a lot of time, depending on the size and complexity of the pipeline. The duration of the inspection will also depend on whether any visible damages or leaks are found, and how extensive the repairs or maintenance work required is. It’s important that the LMP has a clear idea of how long the inspection will take before he or she starts.
The LMP must submit the GPS1 to the building owner within 30 days of inspection. If the building requires any repair, the LMP must file a certification of correction to the DOB within 120 days of the initial inspection date (though this deadline can be extended by 60 days).
If your gas piping inspector finds any issues that pose an immediate danger to tenants’ safety, your gas will be shut off and the utility company will be called. You will then have up to 120 days to remedy the situation and resubmit a new Certificate of Correction signed and sealed by your LMP.
To ensure your pipeline is properly inspected, hire only qualified professionals. According to the city’s rules, only Licensed Master Plumbers (LMP) or individuals who have at least five years of full-time experience working under an LMP’s direct and continuing supervision can conduct gas piping inspections.
Check for High Pressure
Gas is an efficient, cost-effective way to power heating systems and other appliances. But, it can also be dangerous if a pipe corrodes or develops a leak. That’s why the City recently implemented Local Law 152, requiring that property owners have their gas piping system inspected by a qualified inspector at least once every four years.
During the inspection, the inspector must visually check all public exposed gas piping (including outside gas piping) and test each one with a portable combustible gas detector. In addition, the inspector must also check any rooms or spaces within the building that contain gas piping or gas utilization equipment (including mechanical and boiler rooms).
The qualified inspector must also send the building owner a GPS1 Gas Piping Periodic Inspection Report within 30 days of conducting the inspection. This report must describe all conditions observed during the inspection and indicate any corrections that are necessary. Within 60 days of the GPS1 report, the building owner must submit a GPS2 Gas Piping System Periodic Inspection Certification to the Department of Buildings, through a web portal specifically created for this purpose.
Aside from checking for potential hazards, the inspector must also inspect for signs of excessive atmospheric corrosion or piping deterioration; illegal connections; non-code compliant installations; and other conditions listed in LL152 regulations. If an inspector identifies any of these conditions, the building owner must notify the utility company and DOB immediately.
Once the report is submitted to the DOB, the building owner has 120 days to correct any conditions identified in the inspection. After that, the inspector must send another GPS2 report to the DOB indicating that all corrections have been made.
While the LL152 regulations provide an in-depth set of requirements, they can be overwhelming and confusing for a busy property manager or building owner. Using a tool like Xenia can help simplify the process of managing gas line inspections, ensure that the required inspections are being conducted on time, and that the appropriate documentation is being filed with the DOB. Xenia’s cloud-based platform allows for rapid task assignment and tracking, as well as easy-to-use document attachments. This helps to streamline the gas piping inspection process, minimizes errors, and improves data quality and reach.
Check for Low Pressure
As part of a gas piping inspection, a professional will also check your building’s gas pressure. Overuse of appliances or leaks in the system can cause the pressure to drop. A sudden drop in pressure indicates that there is a leak and needs to be addressed. The engineer will test the gas pressure using an air, CO2, or nitrogen pressure test. The piping will be pressurized to a level that is at least 1 1/2 times the maximum working pressure and held at the test pressure for a minimum of 15 minutes.
If the pressure drops significantly, your inspector will note it on a Gas Piping Inspection Certification (GPS2) submission to the DOB within 60 days of the inspection date. This report will contain all observed conditions and identifies corrections, if any, that need to be made.
The inspection also looks at the condition of your building’s gas meter and regulator. If they’re not in good shape, the engineer may recommend that you replace them. They’ll also check whether there is sufficient ventilation in the area where you keep your gas equipment, which is vital for safety.
If anything dangerous is found during the inspection, your gas will be turned off and the fire department will be called. All normal precautions, like not switching on any electronic devices, should be taken until the fire department has responded and declared the area safe to use.
You’ll need to have your gas piping inspection done every four years, or more often if there is damage or a risk of a dangerous situation. Only a licensed master plumber or people with the right qualifications working under a master plumber can perform these inspections. The DOB has a list of qualified vendors online that can help you find one. Once the inspection is complete, you’ll need to submit a GPS2 through the DOB’s web portal. You’ll need to keep all documentation related to your gas piping inspections for 10 years. If you have any questions about your next inspection, the DOB has a FAQ page that can help.